It’s 5:45 AM when the work shift starts at the Bike Fun International (BFI) factory. The overhead lights illuminate 11 production lines in the spacious hall. Two lines are fully occupied with the production of Superior bikes. Nearly 200,000 bicycles and e-bikes are produced in Kopřivnice annually, with Superior accounting for about a quarter of total production. In addition to in-house development, in-house paint shop, and production of Superior, Rock Machine and Frappé bikes, BFI concern also develops its own Sport Drive electric drive system and cycling accessories under the ONE Bikeparts brand.
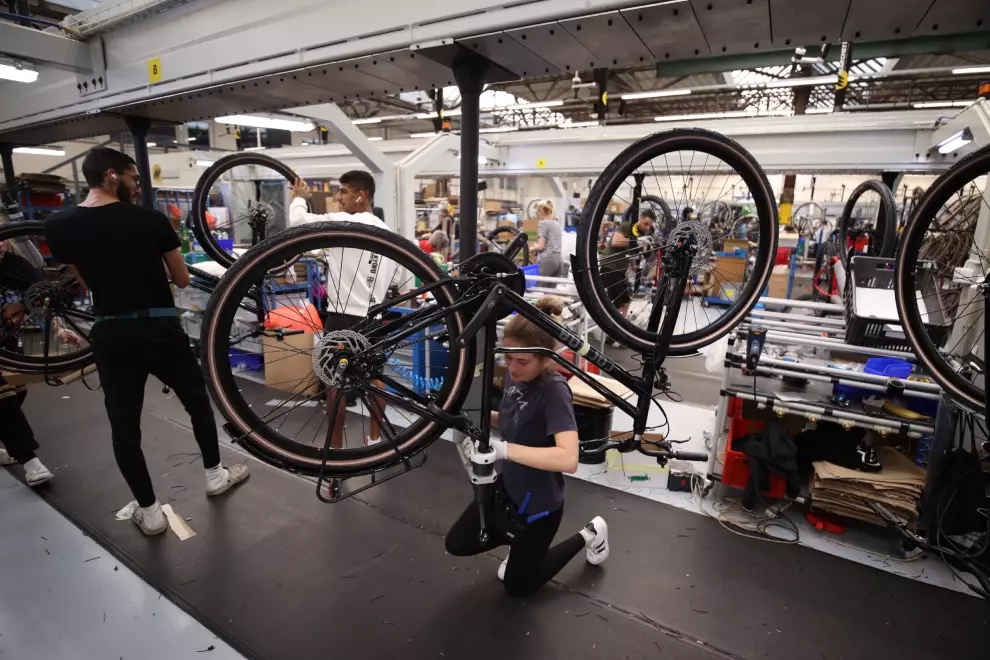
“Everyone in the factory is mad about cycling,” Superior marketing manager Ondřej Cedidla says. Over 60 employees join every year’s May Bike to Work Challenge, and many watch MTB World Cup races or Tour de France stages together. Traditionally, the race in Nové Město na Moravě is the most popular event among employees. Mr Cedidla reminds us that this year, the company departed a whole bus for employees and their families to see the World Cup race with their own eyes. Who were they cheering for?
Obviously, everyone was rooting for the international jb BRUNEX Superior Factory Racing Team members. Side by side with the local rider Simona Spěšná, the three-time world champion Ramona Forchini from Switzerland also wears the factory team’s jersey. “Knowledge gained at the top races is transferred to our developing department to improve the future Superior bikes,” explains Superior’s product manager Petr Lavicka.
https://www.instagram.com/p/CuzJ4Iysng4/?img_index=1
According to Mr Lavicka, the development of new Superior models stretches over three years, with testing taking most of the last year. The racers share their findings with designers and engineers regarding frame handling and their experience with individual components.
“Superior’s bikes are designed to meet all the points of our fundamental triangle, with low weight, modern design and functionality at the apex of the triangle,” says Superior product manager Petr Lavicka. He was among those who decided that Superior become the first European brand to put bikes with 29” wheels in mass production back in 2004.
Whereas in the past, the designers drew frames on drawing boards, the process is completely left to computers as Superior bikes are designed in 3D design programmes. Trends and possible future solutions are suggested by designers in sketches. Designers select the most promising designs and refine them until they meet the technological requirements of series production.
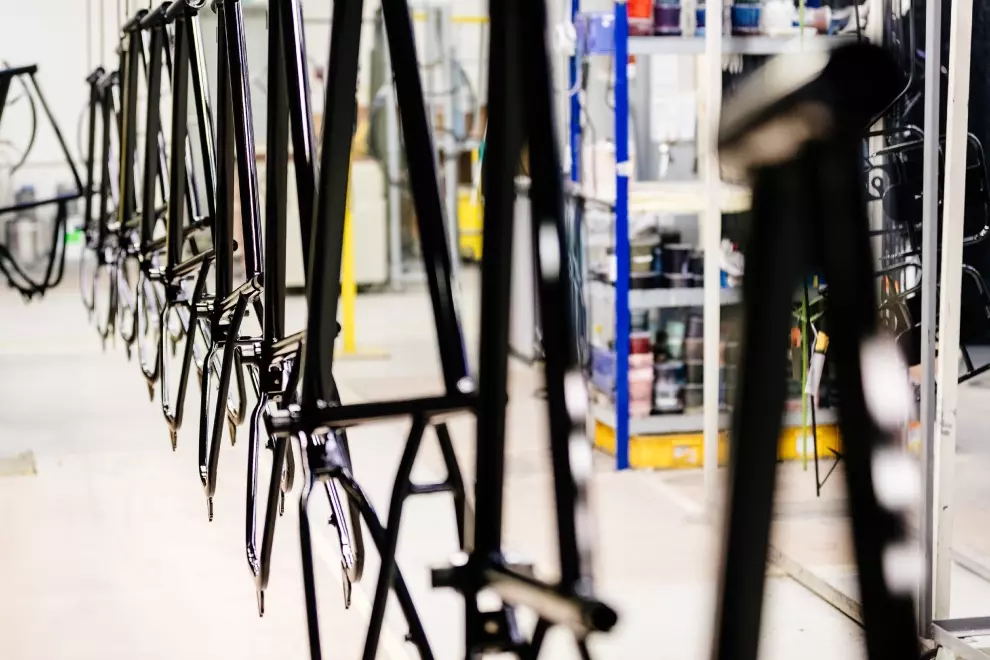
In the following steps, details, material thicknesses or manufacturing tolerances are resolved, suppliers are selected, and the first prototype samples are built. At this stage, the development department is assisted by 3D printing, which saves a great deal of cost and reveals any errors much more clearly than a computer model. The frame of the upcoming bike then undergoes strength and other tests before its final form goes into mass production. While Superior is in charge of the developing process from beginning to end, the frame production itself takes place in carefully selected factories in Taiwan or Europe.
“As carbon is becoming more and more popular among sporty riders, the ratio of bikes sold with carbon and aluminium frames is now 1:1,” says Petr Lavička. Along with carbon, there is also a significant increase in demand for lightweight sports electric bikes.
Currently, 11 production lines are in operation in Kopřivnice, all of which can complete every type of bike. “However, it is an unwritten rule that each brand has its own lines. Superior bikes are assembled on two permanent lines where the staff meets specific requirements associated with this brand, such as routing brake cables through the frame or way of lubrication,” Petr Lavička says.
Before entering the production line, operators mount frames to the conveyor that moves them slowly between the workstations. Proceeding on the production line eliminates the risk of frame abrasion or damage when passing it hand to hand. With the advent of electric bike manufacturing, new workstations were added to provide advanced programming and tuning of the electric motor.
At each station, there is something next to attach. In the first stage, the frames are equipped with bearings. Then the cables and rear brake hoses are put in, followed by the fork, stem, handlebars, brakes, cranks, derailleur and chain. During the process, dozens of people put their hands on each bike. Each worker must perform the operation in a given time to keep the line running smoothly and avoid idling.
In the production hall, also the wheels are assembled, using rims, hubs, nipples and spokes. The manually knitted wheels are fed into an automatic machine that guarantees desired spoke tension and precise centring.
Superior is committed to the quality of the parts, with quality control varying from supplier to supplier, depending on experience. For some suppliers, inspection is spot-checked, while for others, every part is checked. In the final stage, the bikes are packed into boxes and handed over for dispatch. Each model has a precise packaging method, whereby the individual elements are wrapped with protective cardboard or cushioning foam and placed in a box.
“We believe that only hard work can move us forward. That is also the main reason why we put so much effort into our own development. We are most motivated by the results of our race team but we are equally concerned about happy customers, whether they are passionate athletes or amateurs riding for fun. In all cases, we strive for the most important thing – that the bikes we build are always Superior,” Marketing Manager Ondrej Cedidla says.